Polywater PowerPatch® Seals Beat Common Gasket Replacement Methods
How a company used PowerPatch to reduce the cost and downtime of a transformer main gasket leak.
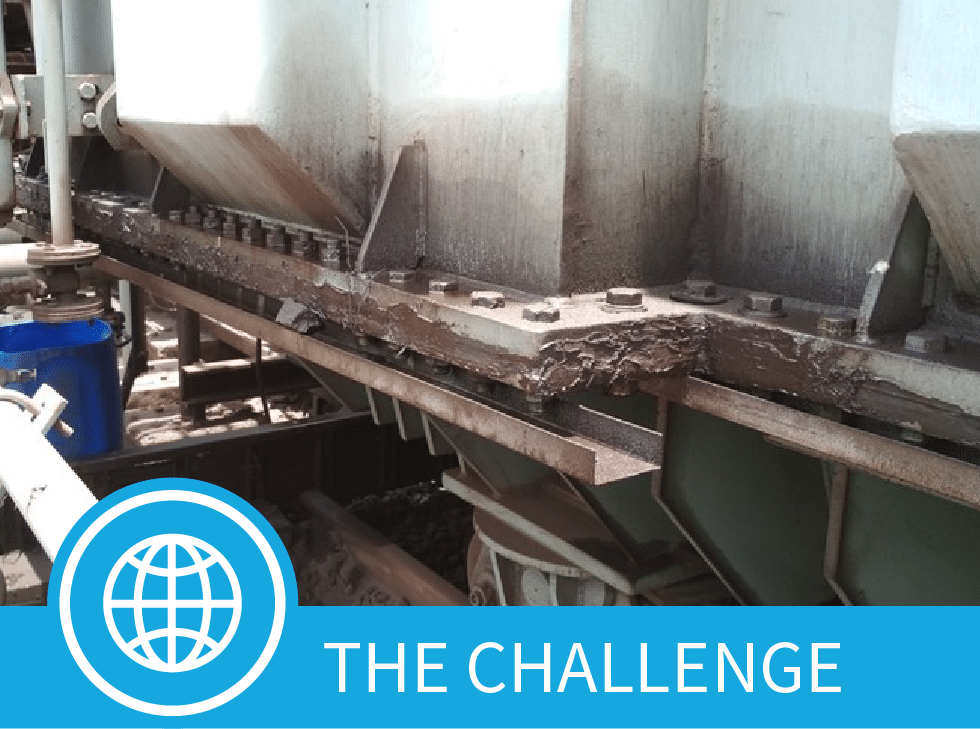
Minimize Moisture to Core
Oil leakage from the Bell Tank gasket and fastening bolts of a 260 MVA generating transformer posed a serious concern for a power generating utility. The asset manager was hesitant to expose the transformer core to atmospheric oxygen and moisture as is the case when traditional gasket replacement practices are used. Exposure to moisture and atmospheric gases creates deleterious interactions with the solid insulation and insulating oil, which can often cause premature failure of the transformer. The utility needed a sealant technology that allowed for the leak to be stopped in-situ without exposing the insulating oil and paper to these elements when lifting the bell tank needed before the gasket replacement process was to begin.
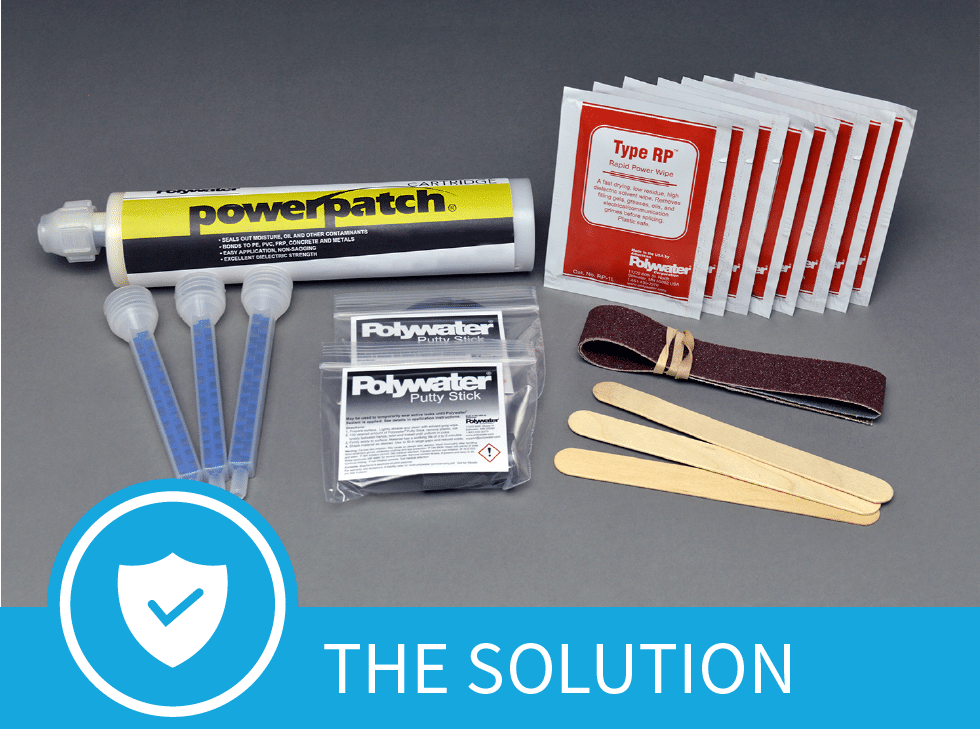
PowerPatch Transformer Sealant
The utility contacted a service company specializing in leak repair, which recommended the use of Polywater PowerPatch® – a specialty sealant designed to arrest active oil and SF6 gas leaks in transformers. A site visit was made to determine the amount of sealant required and to assess any points of limited access to the targeted seal area. The perimeter of the gasket was approximately 18 m in length and contained over 200 bolts, many of which had been over-tightened and leaked. The service company determined that the full perimeter and all bolts should be sealed with PowerPatch to ensure future leaks would not occur through unsealed areas once the pressure was restored.
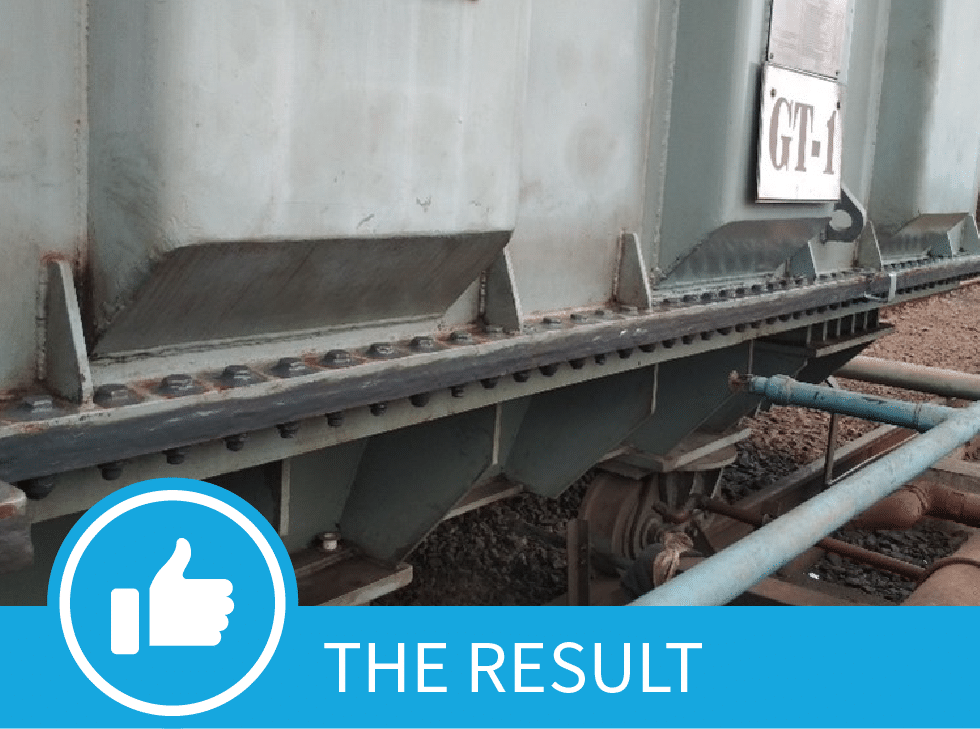
PowerPatch Saves Time and Money
The service team was dispatched to the site to perform the repair. PowerPatch was applied to the entire gasket perimeter along with all bolts and nuts. Once completely sealed, the transformer was immediately put into operation and did not require any further maintenance.
As required by the utility, the sealing of this critical asset with PowerPatch, minimized the risks to oil and solid insulation from accelerated aging and premature failure. The on-site application of PowerPatch, allowed the power utility to reduce expenses significantly. PowerPatch helped to avoid transportation, heavy lifting equipment, power-shut down, oil removal and re-conditioning costs over gasket replacement.
Read full story here: Transformer Leak Repair Story from Polywater®