The Origins of Lubrication in Cable Blowing: An Interview with Expert Willem Griffioen
Willem details how chemical specialization of lubricants helped advance a revolutionary mechanical installation method of communications cables.
What Albert Einstein was to theoretical physics and quantum mechanics, Willem Griffioen is to practical physics and cable jetting mechanics. While that may be a bit of hyperbole, Willem did make significant contributions worthy of recognition and celebration. He literally invented the machine and much of the fundamental technology now known in the communications industry as cable jetting or cable blowing, in which cable—most commonly fiber optics—is dragged and pushed into conduit via the force of compressed air, rather than connected to a winch and pulled in by brute force from the far end. This concept of cable installation was considered radical when first introduced in the 1980s, but is now a ubiquitous, global methodology familiar to virtually every craftsperson in the trade. Willem recognized early on that a critical component of successful jetting is proper lubrication. However, when iterations of common cable pulling lubricant formulas failed to maximize the potential of Willem’s new blowing machines, he connected with Polywater for chemical assistance.
In this Q&A, The Transmission sits down with Willem Griffioen, Ph.D., Senior Engineer at Plumettaz S.A. to explore the relevancy in today’s market of his groundbreaking invention, related technical research papers, and the early collaboration with Polywater in the development of the specialty lubricants to optimize installations. A few highlights from the interview can be seen in the video below. For the full interview, continue scrolling.
Q. Welcome, Willem. We are honored to speak with you. Can you first provide your educational background?
A. My graduate education started at Leiden University* where I studied physics and mathematics and did four years of unfinished PhD work. I was honored that my genius Italian professor selected me to do new research on the low-temperature physics of superfluid helium-3 and even hopefully bring the Nobel Prize back to the university. I learned a lot there but decided not to continue and instead went to work for the Dutch PTT** in late 1984, where roughly a year later I invented cable blowing. I did get my PhD later in fiber reliability, so that was okay.
Q. We’re certainly glad you decided to abandon that earlier superfluid helium-3 quest and focus your talents on communications. Your contributions to the industry have been consequential, to say the least. Can you describe your work history and current title?
A. I started working for the Dutch PTT research lab, spent time at Draka Comteq, Ericsson Cables, and am now Senior Engineer for Plumettaz.
Related Content: Q&A: The Effect of Pulling Lubricants on High Frequency Data Cable |
Q. You are considered by many to be the father of cable jetting technology, having developed the first cable jetting machine for the Dutch PTT. Can you describe how that came about?
A. In 1986 the PTT could not easily install cables by pulling. The operations department could calculate straight sections, gravity, friction coefficients, and the capstan effect, but they could not make sense of the limited pulling lengths. They could pull only 300 meters maximum, despite predictions that longer pulls were possible. To accomplish a 2.1-kilometer pull, it was necessary to split the length into two times six 175-meter sections with two times five intermediate-assist figure-8 capstans. Pulls were started in the middle and moved outward to the two ends, but there were synchronization problems with the winch and capstans. This was terrible work to do, and very expensive. It was so time-consuming that often only one direction could be done in a day, and in the morning the remaining cable would sometimes be gone, taken by copper thieves who weren’t up to speed, so to speak, on fiber optic cable.
The central department of the PTT believed the limiting factor was cable stiffness, and they asked me to model that, which I did. I found the formulas and calculated that it was only a minor factor, not the reason the pulling was so difficult. I also found that the capstan effect from duct undulations is what really kills you. This led me to investigate cable blowing as an installation method, and the rest is history.
Q. Your 2022 paper, “Cable Blowing — 35-Year Historical Review”, states that British Telcom developed the “blown fiber technique” in 1982. What differentiates your methodology from that? What was your contribution that advanced the technology?
A. Yes, British Telcom invented blown fiber. The trick was to have high-speed airflow in the duct along the flexible fiber member. This generated uniform drag over the length of cable, which was a propelling force that compensated, locally, for the gravity friction. This avoided tension buildup in the cable, and there was no capstan effect—exactly what we needed. But no one ever thought it would be possible to blow a real cable because it was considered that only lightweight and flexible fiber members could be installed by blowing. And you were not allowed to push such flexible fiber members because of the risk of damage. A detector would shut down the machine when it sensed buckling caused by pushing. I calculated that it would actually be possible to blow real cables; that there was also a benefit of pushing the cable I found in the first test, which I’ll explain later.
Related Content: FAQ – Cable Pulling, Lubrication, and Tension |
We tested my theory in Kootwijk, the Netherlands, at a radio station for the Dutch PTT. They had four duct loops in a test field used earlier to test four figure-8 capstans in cascade. I said we can go through two loops with blowing. Everyone else said that‘s not possible; it’s already been tried, and it fails. But their technique involved a piston at the end, so no distributed drag forces of high-speed airflow to overcome gravity friction and avoiding axial force build-up, hence avoiding the capstan effect. Also, no mechanical pushing was done to feed the cable into the pressure zone, so back pressure force was not compensated and the capstan effect was already large from the start. So, indeed, that would not work.
My idea was to eliminate the pig [piston], like with BT’s blown fiber, and to push the cable as it’s blown. We had to do this by hand, as there was no machine then, of course. There were four of us pushing, turn by turn. I was one of them. It was very hard and there was a lot of complaining. After we blew through one loop, though, the doubters went silent. When two loops went through, they said, “It’s a miracle!”
The fact that they said it’s a miracle indicates that it was something novel and already the basis for a patent. It was an unexpected success—but not for me, because I had calculated this. We kept blowing and managed to get through the third loop and even the fourth loop. Then it was a miracle even to me because I had not predicted that.
Q. Is it fair, then, to say that you took a theoretical technology and turned it into a practical reality with your additional calculations, modeling, and the invention of the actual machine?
A. My theory was that propelling forces from blowing would be sufficient to reach two loops, and that stiff cables weren’t a problem. I had modeled that a certain stiffness is actually needed to allow pushing. What I discovered after succeeding with the third and fourth loop was that it was not a uniform air drag force as assumed by British Telecom. Rather, since it is compressible, the air was expanding towards the end, gaining velocity and exerting much higher force. The air drag forces were minimal at the beginning and at the end they were amply sufficient. Thus, to assist the cable by pushing, on top of the force to feed the cable into the pressure zone (when pushing by hand we had no idea how hard we pushed), you can bridge the first length where blowing alone is not sufficient to compensate for gravity friction by some percentage of pushing until the drag forces of the expanding air flow down the conduit are large enough to take over. My aha moment–and the basis for the patent in 1987—was realizing that jetting is the synergy of pushing and blowing. Which it really is. If blowing only would reach 50% of the length and pushing only 25%, then the jetting synergy makes it 100%, thus doubling the length of blowing alone, both in the model and in practice.
Q. And you developed the first blowing machine about that time?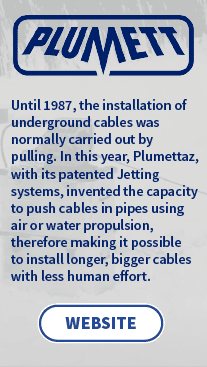
A. Yes, we made the first machine in the workshop with no drawings. It was field tested on a real installation, and it helped so much that we didn’t get the machine back. They requested four more machines for use in tandem for better production. So, we then developed drawings and constructed four machines in two months, which then for me seemed like such a long time. I was still ignorant of how long such things take in the real world.
We eventually delivered the four machines but didn’t get those back either. In fact, we had to make thirty more. They became very popular very quickly. Within four months there was no one pulling cable in the Netherlands anymore. This was a governmental organization—the Dutch PTT—switching methods this fast, so there was obviously a big need. The blowing machine came at the right time. It was a transformation, a revolutionary technology. And they were very happy with me for inventing the CableJet™ machine. I received the Diana Award*** for that scientific achievement.
Q. When did it become apparent that lubrication was needed in the jetting process, and what led to the conclusion that existing lubricants were insufficient?
A. Paraffin oil was already in use for cable pulling in the Netherlands, and so that’s what we started using for blowing as well. I remember that for pulling, a crude box filled with foam soaked in paraffin oil was used. The cable was dragged through the box to apply the lubricant, but that wouldn’t work for blowing because it was hard enough to push a dry cable, let alone a lubricated one. You couldn’t get a grip on it. What we did instead was simply pour oil into the conduit where it was spread by the action of the air flow, and that worked somewhat, but only to 700 meters with the cables of the day, which are different than they are now, of course.
Related Content: Coefficient of Friction in Cable Pulling — Part 1 |
The first problem we encountered with paraffin oil was in Spain with the Madrid-Sevilla link for the World Expo. Exclusive worldwide license for the CableJet™ blowing machine had been sold to Plumettaz S.A., and they were building the prototype. The machine, still the PTT one, was working well in field tests in Madrid, but not in actual installations. The cable would stop prematurely. Gerard Plumettaz thought that the spreading of the lubricant was inadequate, so he went to the far end of the conduit to see what was happening. He slipped into the manhole and the first thing he did was put his hand over the end of the duct. He could feel that there was no lubricant, which was typically evident in the form of a mist. But the air was coming out dry. The conduit in Spain was larger than the conduit in The Netherlands and the problem was solved by pouring in three times as much lubricant, spreading the lubricant fast enough. The installation was completed successfully, but still with max 700 meters blowing distance. Our ultimate goal, of course, was to extend the length of installation, and that simply wasn’t possible with paraffin oil.
Q. The shortcoming of paraffin oil was thus in the ability to apply it?
A. We found that we could distribute the oil faster if we used more oil, but the blowing distance remained limited. We also found that over time the paraffin oil residue became tacky. This was a real problem later if the customer wanted to blow in more fiber or microducts to take advantage of a higher conduit fill percentage. The sticky residue limited the distance we could blow.
We also tried to blow with Polywater® J or Polywater® F pulling lubricant—I don’t recall which—because it was recommended as the best in the world. We were expecting good results because we felt the material with our fingers and thought it was so slippery, you know, that it must be very good. But when we tried it, the cable stopped short. We again went to the end of the pipe and this time, not only was there no lubricant coming out, now there was also no air. We waited and eventually there was a swoosh and a big load of foamy lubricant sprayed out, almost hitting the nearby railroad tracks. We joked that maybe a train would derail. The compressed air had caused the lubricant to foam up into a big mess. So, we realized that pulling lubricants were unsuitable and a specialized lubricant was needed to optimize installation distance.
Q. How did you connect with Polywater in the quest for help with lubricant specialization?
A. The first connection with Polywater was in 1987. I met John Fee**** at the International Wire & Cable Symposium in Arlington, Virginia. He was there to present a paper on the combustibility of pulling lubricant residue. I talked with John about cable blowing, which we were already doing, but could not present it that year at the conference because the abstract due date was before we filed the patent. He took me to see an actual cable pull in nearby Washington D.C. That was my first contact with John. He was keenly interested in the technology and its potential for improvement. This led, later after the “foam incident” and with involvement of Gerard Plumettaz, to the birth of cable jetting lubricant, which was commercialized as Polywater® Prelube 2000™, and soon followed by Plumettaz’s chemically similar CJL jetting lube. That resulted in a huge leap forward in cable installation lengths.
Q. Did you help lay out the parameters for Polywater on what this special lubricant should do?
A. I only described the problem. We knew there was an issue with the use of cable pulling lubricants because of foaming, and I reported my findings to John.
Q. Were you ultimately involved in the testing of Polywater’s prototype lubricants?
A. Not so much early on during the critical development phase. Most of the interaction occurred between Plumettaz and Polywater. I always had contact with Plumettaz, but I was working on other things. Plumettaz found that Polywater’s Prelube was the best lubricant. They developed the technique of spreading lubricant by blowing a foam pig through the conduit for better distribution. Polywater delivered the product and Plumettaz designed the process. Later, of course, I was heavily involved in lubrication when I invented the lubricator device for the blowing machine. That was a Draka invention, as I was working there then. I visited Polywater in Minnesota with Maya Keijzer in conjunction with that project. I have a fond recollection of John Fee taking us ice fishing on a frozen lake. It was very cold.
Q. How critical is the use of lubricant to successful cable jetting?
A. It is absolutely integral. Without proper lubrication jetting distances would be limited to maybe a third of what is regularly achieved today. Even in microducts with low-friction liners you can see a 50% gain in distance. Jetting is simply not practical without specialized lubricant and proper application. It is certainly not advisable.
Q. Would the industry have even adopted blowing technology without the simultaneous development of a specialty blowing lubricant?
A. Probably not to the degree that it has. This is a hypothetical question, of course, but it’s hard to imagine something being as popular if it’s two or three times less effective. Certainly when the pulling “competition” was using Polywater lubricant.
Related Content: How to Avoid Crushing Fiber Cable During Installation |
Q. What are the potential consequences of improper or inadequate lubrication in jetting?
A. There are alternatives to Plumettaz CJL or MJL and Polywater Prelube on the market, but they are penny-wise and pound-foolish. Trying to blow cable without lubricant for anything other than very short distances is equally silly. You can’t blow the cable far enough. It gets stuck. Then you have to dig. This gets very expensive, and any perceived savings in lubricant evaporate very quickly. These lubricants are cheap insurance. We treasure those small bottles.
Q. In your opinion then, Prelube and CableJet lubricants still meet modern cable jetting needs?
A. Yes, they are the best available. I am a physicist, not a chemist. I don’t know the formulation secrets, but we have tested several lubricants and these are still there at the top, still the cream of the crop of jetting lubes. It is important to select the right one, though. It is difficult to get a viscous lubricant spread throughout a microduct, for example. Specialty lubricants for microducts are formulated with lower viscosity and specialized chemistry that allows them to coat further under this unique jetting condition.
Q. How much of the success in spreading lubricant thinly in microtubes do you attribute to the lubricant itself versus your Plumettaz applicators?
A. Well, I don’t know but clearly the best performance comes from the use of both. The lubricator offers the mechanical assistance by distributing a very thin film of lubricant on the cable, and the lube contributes from a chemical standpoint. The viscosity of the lubricant plays a major role.
We tested this viscosity problem by blowing lubricant with a foam pig through a 1,500-meter duct. Then we took out samples every 100 meters to analyze the lubrication, which was perfect for the first 300 meters, but then it declined. By 400 meters it was greatly diminished, and after that there was no lubricant distributed at all. The solution for these long installations was a larger foam pig with more lubricant. We call that rich lubrication. We apply enough so that although you’re depositing lubricant throughout the conduit, there is still some at the end when the pig exits the duct. This is a long, viscous column of lubricant in the duct, though, maybe two meters long, so it takes time to blow it through under pressure. You only do this if you really need it.
I remember we demonstrated this for a customer in Stockholm, and we waited and waited—even took a lunch break, waiting for the foam pig to exit the end of the duct with the lubricant. Finally, the pig pops out and then we were able to blow in the cable in a split second. But we never heard from that customer again. They only remembered the lubrication process.
Q. Your 2012 paper, “Cable in Duct Installation: Lubrication Makes the Difference”, mentions electrical static charge and condensation clogs as limiting factors in jetting length solved by lubricant choice. Can you describe these terms?
A. We discovered that as the cable moves through the duct it generates an electrical static charge. This charge pushes the cable against the inner wall of the duct, increasing friction. This is dependent on the speed of the installation, so the faster the cable moves the greater the charge. To some extent we could control this by reducing the blowing speed. Although we did not study this phenomenon in depth, we did discover that the application of lubricant with the CableJet applicator eliminated the charge, so the problem was solved. We didn’t have to investigate why it worked. We just knew it worked.
The condensation clogs occur with the small cables if you use an air compressor without an aftercooler. Humidity also plays a role. There can be a lot of moisture in the air. As water condenses, it collects and sticks to the inner walls of the polyethylene tube, adding tension. It creates a capillary action and essentially glues the small cables to the tube wall, increasing friction. But again, the use of specialty lubricant through the CableJet applicator eliminates the problem, especially with an aftercooler (if not, you might have large amounts of water, which still affects blowing negatively). Then we don’t have to pay much attention to it.
Q. Do all Plumettaz blowing machines now incorporate special lubricators and reservoirs to accommodate these optimal lubrication methods?
A. Unfortunately there are still customers who need to discover the advantage of these add-on features. I don’t know the percentage of machines we sell with lubricators, but the percentage can and should grow, especially for installing small cables. Even though we do not have a cable lubricator which you can build in all machines, we do have one for every machine, simply by placing them “on-line” in the duct immediately after the blowing machine.
Q. Polywater had one of the first Plumettaz machines in the U.S. for lubricant development purposes, and a major cable manufacturer approached us to ensure the machine was suitable for their cable. Of course, it was fine. All these years later, cable manufacturers now require that new cables meet blowing tests. In other words, machines were once designed for the cables. Now cables are designed for the machines.
A. Yes, an interesting observation. Things have come full circle. Of course, you still have to have the right machine for your cable. For example, the Plumettaz SuperJet™ has a three-position setting for proper sidewall pressure control. Too much sidewall pressure can exceed the cable’s crush resistance. Our competitors do not have that.
Related Content: Planning Cabling Projects Improves Success and Safety |
Q. Have the performance criteria for a good jetting lubricant changed over time?
A. I don’t think the basic parameters have changed. The lubricant has to significantly reduce both hydrodynamic and boundary friction. It has to reduce not only the initial tension, but it has to offer long-term performance. In other words, it can’t dry out as it’s blown far down the conduit with all that air. It obviously has to be compatible with the cable and duct. It has to apply easily through the lubricators. It should have low toxicity for worker safety and make low environmental impact. It has to eliminate static charge and help prevent condensation clogs. It has to resist foaming. And these can’t just be manufacturer claims; there should be testing documentation available. I don’t know of any improvements that can be made unless it’s to further reduce friction.
On this point about whether the lubricant dries out, I think your specifications state that Prelube retains 90% of its lubricity after evaporation. We also studied this in our most challenging testing experience for CERN, where installed cables have to be blown out and new cables blown in—in one case even a year later, and after giving it a high radiation dose. What do you think the results were? It was blowing even better, out and in! So, a lubricant with a slippery dried residue is fantastic.
Q. What percentage of fiber cables are installed via blowing vs. pulling today?
A. I’m not in sales, of course, but I think in the U.S. that only half of the cables are blown in, but elsewhere in the world we find countries where almost 100% of the cables are blown in, whereas other countries have still to introduce the method. Nevertheless, you will find jetting all over the planet, from Iceland to South Africa, in beloved areas by tourists such as the Fiji Islands or in the harshest environment of Alaska. In Europe, a very large proportion of fiber cable is not pulled anymore. Jetting has become the predominate method of installation. It is an enormous success.
Blowing offers other advantages beyond longer installations. The method is more friendly. You can keep all your equipment at one end of the duct. You don’t need to install a winch line. There are all these things you don’t have to do. You can just stay in one place and blow in all the directions you need to go. It’s so much simpler.
Q. It has now been roughly 35 years since you invented the blowing machine. What is the state of cable blowing today?
A. There is, of course, much more cable blowing than in the past. The technology has completely transformed how cable is installed. Most of the development today is aimed at creating intelligent machines. This entails collecting data throughout the installation, such as air pressure, pushing force, cable slip, etc. Monitor and record; that is the new paradigm. Intelligent machines also include sensors that shut the installation down if, for example, an established pushing force is exceeded or cable slip occurs. We’ve come a long way. Plumettaz now makes the IntelliJet™ and OptiJet™ blowing machines that come with an integrated computer and embedded software connected in the field to an IoT platform with additional digital services. We are working on fully automatic machines next. You push a button and, voilà, the machine chooses the right parameters. It automatically creates harmony between the air pressure and the mechanical pushing force to overcome back pressure. There are more advances to come.
Related Content: Lubricant Installation Guide-Communication Cable Pulling & Blowing |
Q. Your 2022 paper mentions a 5.3 km jetting installation. Do you think that’s still the longest uninterrupted blow on record?
A. As far as I know, but I believe that was a downhill blow assisted somewhat by gravity. Of course, in the beginning we could only manage 175 meters. By the time I wrote my lubrication paper in 2012 the record was 3.7 kilometers. That’s an incredible improvement. Distance isn’t the only advancement, though. Fiber counts have increased, and duct filling rates have gone from 30% to as high as 80%. When you combine the longer distances with the higher fiber capacity, blowing technology has experienced an astounding upgrade. For example, the first cables blown in the Netherlands contained only 6 fibers and the ducts were listed as completed. Much later, when capacity need had grown, two microducts 10/8 mm were blown over the old cable and in those microducts two cables with 96 fibers each, so an upgrade of 3,200%. By the way, the new cables could be blown into the microducts with single-shot lengths of 1,500 meters, compared to 700 meters of the original cable that had amply more duct space.
Q. Willem, you certainly made a substantial impact on cable installation technology and the industry as a whole. We hope posterity recognizes the contributions you’ve made and celebrates you as the pioneer you are. We appreciate you taking time to talk with us today.
A. It has been my pleasure. Thank you for having me.
Have any questions?
* Founded in 1575 in The Netherlands—one of Europe’s leading international research universities.
** Posterijen, Telegrafie en Telefonie (in English: Post, Telegraphy and Telephony)
*** Named after the Roman and Hellenic goddess Diana, patron of hunters, meant to symbolize and venerate the hunt for knowledge.
**** John Fee was then president and technical director for Polywater.
Related Resources:
Willem Griffioen. 2012. Cable in Duct Installation: Lubrication Makes the Difference
Willem Griffioen. 2022. Cable Blowing — 35-Year Historical Review